Increased Productivity and Safety When Moving Heavy Equipment and Components
About The Company
Founded in 1983, St. Onge has transformed into a distinguished global authority in supply chain strategy and logistics, serving various sectors including healthcare, manufacturing, food & beverage, automotive, electronics, oil & gas, and more. Their solutions enable businesses to increase profitability, agility, and adaptability. Through research, advanced modeling, design, and engineering, St. Onge optimizes operations strategies, tailoring solutions to individual client needs for improved market positions, ROI, and end-to-end efficiency. Their international footprint, demonstrated by the Global Connexions initiative, provides clients with access to dedicated supply chain experts worldwide for comprehensive and unbiased support.
Load Specifications
Various Equipment & components
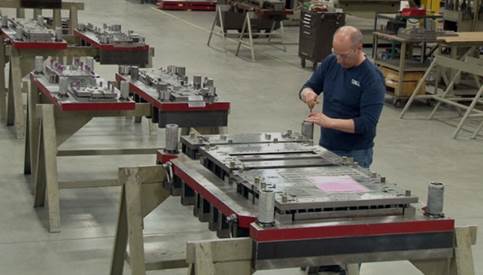
Application Analysis
General Specifications:
- 15′ bridge
- 60′-68′ runway
- 14′ under hook
- Options for 1-ton – 2-ton capacity
- Manual push trolley bridge
- Powered electric chain hoist

Handling Issues
Client needed an overhead crane to service his tool and die shop where they repair and refurbish their client’s equipment and machinery of various types. Onge had been using a fork truck to do the heavy lifting which was slow and unsafe when moving in and around the other employees stationed in the work area. Production was slow because the floor lift had multiple duties and wasn’t always readily available. On a few occasions when trying to upright or tilt a machine to gain access the load got away from the forks and caused additional safety damage issues.
The Solution
To help the client meet the desired goals ASE Systems specified an Enclosed Track workstation bridge (see complete specifications below). ASE’s enclosed track is highly ergonomic in that the bridge and trolley movements require only one pound of force by the operator to move a 100-lb load. For this crane, only 20-lbs of force is needed to move a 2,000-lb load. Another great feature of the workstation crane is its ease of installation; anyone without experience can easily install these cranes and they can typically be shipped in one to two weeks after receipt of order. St. Onge Company’s goals of increased productivity and safety were met with the enclosed track workstation bridge crane. WSBC series cranes are available in capacities up to 4,000-lb, with bridge spans up to 34’ and runway lengths over 250-feet.
Key Technologies
Enclosed Track Workstation Bridge
https://asesystemsbackup.lift-assist-devices.com/workstation-cranes/
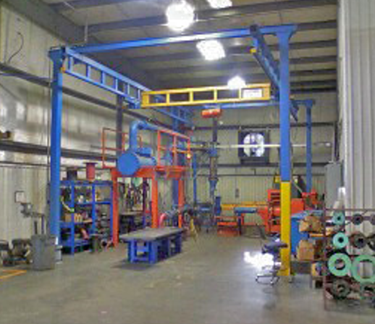